AIM section
MES ASSET INTEGRITY MANAGEMENT
MES Asset Integrity Management provides essential strategies to clients, such as:
- Reliability Availability and Maintenance (RAM);
- Reliability Centered Maintenance (RCM);
- Risk Based Inspection (RBI); and
- Safety Integrity Level (SIL).
Reliability Availability & Maintenance (RAM)
RAM modelling is a simulation method used during the design phase of a capital project to define equipment availability, validate design capacities, and identify sources of excessive downtime or instability in a design prior to equipment purchase.
MES has performed a number of RAM studies of Onshore, Offshore, Subsea and FPSO facilities in the Oil, Gas, Petrochemical and Renewable industries.
MES have sophisticated in-house software tools which have been developed over a number of years and used in the execution of studies. The tool has the following capabilities:
For more information, please click here.
Reliability Centred Maintenance (RCM)
RCM is a process used to identify cost effective maintenance strategies based on a detailed comprehension of a facilities functional requirements, performance standards and conditions of use. MES specialists have the skill base to perform RCM methods, which include:
- Derivation of functional definitions and performance standards
- Analysis of source data to identify trends and failure characteristics
- Failure Modes & Effects Analysis whereby functional failures are defined and failure modes identified together with the consequential effects relative to safety, environmental and system performance
- Based on FMECA results and the failure characteristics of individual equipment and components, derivation of cost effective maintenance strategies can be achieved using:
- on condition maintenance
- on failure maintenance
- scheduled overhaul / replacement fault finding
- redesign where appropriate and cost effective
- Preparation of maintenance documentation including scheduling
The benefits gained from implementing RCM analysis include:
- Maintenance strategies tailored to suit specific commercial and operational requirements
- Optimisation of maintenance costs
- Efficient use of maintenance resources
- A clear audit trail and demonstration of compliance with safety case or other regulatory / legislative requirements regarding the in-service availability of critical equipment
Risk Based Inspection (RBI)
MES has the capabilities to implement Risk-based Inspection (RBI) programmes for clients in Oil & Gas industry. Our experience in Asset Integrity Management enables us to work with each of our clients to provide tailored solutions to meet their unique requirements. RBI can be applied to offshore & onshore installations, as well as FPSOs and pipelines.
Risk based inspection (RBI) is a systematic approach that enables users to make informed business decisions regarding inspection and maintenance expenditure. The fundamental objective of implementing a successful RBI programme is to create an inspection strategy that clearly defines:
- The equipment items which require inspection;
- The optimal periodicity of inspections; and
- The correct techniques that should be performed to identify defects that a particular component is likely to develop.
A schematic of the overall RBI process is shown below:
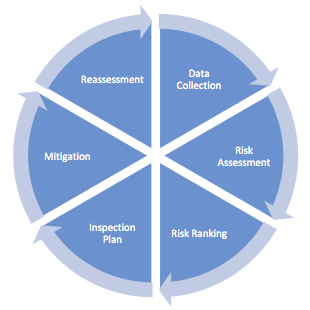
[Based on API-580]
*Risk Assessment includes "Consequence of Failure" and "Probability of Failure" analysis.
The fundamental reasons for implementing RBI are to:
- Measure and understand the risks associated with current inspection programs;
- Provide a basis for shifting resources from lower to higher risk equipment;
- Enhance the cost effectiveness of inspection and maintenance resources;
- Monitor risk reduction as a result of implementing inspection practices;
- Use historical data to facilitate the maintenance planning process for future installations;
- Allow management to review safety in an integrated, cost effective manner;
- Increase reliability of equipment and operation thereby extending asset life; and
- Minimise loss of production through selecting cost effective inspection programs without compromising safety and risk to environment.
Safety Integrity Level (SIL)
This assessment is a risk based approach to determining the required safety integrity levels (SIL) for safety instrumented functions (SIFs). SIL assessments are performed in accordance with IEC 61508 / 61511.
Qualitative and quantitative techniques are adopted to perform SIL assessments, such techniques include:
- Risk Graph
- Layers of protection Analysis (LOPA)
- Fault Tree Analysis (FTA) / Event Tree Analysis (ETA)
MES consultants have significant industry experience and are certified to facilitate SIL workshops.